Taking Full Advantage Of Efficiency and Quality With Cutting-Edge Steel Stamping Strategies
In the world of metal marking, the pursuit of functional excellence via the combination of cutting-edge methods is critical. As sectors progress and needs for accuracy and effectiveness increase, staying ahead of the curve becomes a calculated crucial. By welcoming innovative innovations and procedure improvements, companies can unlock brand-new levels of efficiency and item top quality. The crossway of advanced steel stamping methodologies, automated systems, rigorous high quality controls, and lean manufacturing concepts uses a tantalizing glance right into the future of manufacturing. This convergence holds the guarantee of not just conference yet exceeding market criteria, establishing the stage for unmatched efficiency and consumer fulfillment.
Advanced Metal Stamping Technologies
In the world of steel stamping, the combination of advanced modern technologies has changed the market, enhancing accuracy and performance in producing procedures - Metal Stamping. Advanced metal marking technologies have actually played an essential role in raising the capacities of manufacturers, permitting even more intricate styles and greater manufacturing rates
Among one of the most considerable improvements in metal stamping technology is the implementation of computer system mathematical control (CNC) systems. CNC systems allow accurate control over the stamping procedure, causing constant and accurate production of facility components. In addition, using servo presses has produced enhancements in power efficiency and decreased cycle times, better enhancing the production process.
Furthermore, the assimilation of automation and robotics has streamlined steel stamping operations by enhancing performance and minimizing the risk of mistakes. Automated systems can carry out jobs with rate and accuracy, bring about improved general efficiency in the assembly line.
Automated Processes for Performance
Usage of automated procedures in metal marking operations has actually substantially enhanced performance and efficiency in manufacturing centers (Metal Stamping). Automated systems have changed the steel stamping industry by simplifying processes, reducing manual treatment, and lessening the margin of error. These automated solutions incorporate a series of innovations, including robot arms, CNC makers, and electronic control systems, that work cohesively to perform elaborate stamping jobs with precision and speed
One primary benefit of automated procedures in metal stamping is the consistent quality they supply. By eliminating human error and variations in manufacturing, automated systems make certain that each stamped component satisfies specific requirements with very little problems. Automation allows constant operation, dramatically lowering downtime for tool modifications and upkeep, consequently taking full advantage of general productivity.
In addition, automated procedures boost safety and security in steel marking operations by reducing the need for manual handling of heavy products and sharp devices. This not only safeguards workers but also adds to a much more streamlined and effective process. Finally, the integration of automated find more processes in steel stamping operations is essential for achieving optimum effectiveness, high quality, and safety criteria in modern-day manufacturing environments.
Quality Assurance Procedures in Stamping
Provided the emphasis on consistent high quality and effectiveness accomplished with automated processes in metal stamping operations, executing robust high quality control steps ends up being critical to promote standards and guarantee precision in stamped components. Quality control in metal stamping includes a multi-faceted technique to assure the reliability and accuracy of the last products. By integrating these procedures right into metal stamping operations, suppliers can continually generate high-grade stamped components that satisfy the strict requirements of modern-day markets.
Enhancing Precision Through Technology
To attain unmatched accuracy in metal stamping processes, introducing developments are constantly being developed and integrated into the production operations. Advanced modern technologies such as laser cutting systems and computer system numerical control (CNC) machines have changed the way metal elements are stamped with utmost precision. By making use of laser reducing modern technology, suppliers can achieve detailed article and complicated designs with micron-level precision, making sure that each stamped component fulfills the most strict top quality standards.

Moreover, the use of simulation software program allows producers to examine and maximize marking processes before actual manufacturing, recognizing possible areas for improvement and make improvements criteria to attain optimum precision. By embracing these ingenious modern technologies, suppliers can boost accuracy, increase efficiency, and supply top quality stamped products that fulfill the most strict requirements of modern-day markets.
Executing Lean Manufacturing Practices
Integrating lean manufacturing practices into metal marking operations can lead to streamlined manufacturing procedures and enhanced overall performance. By focusing on removing waste, maximizing resources, and constantly boosting processes, steel marking business can boost efficiency and quality while minimizing expenses.
In addition, lean manufacturing techniques encourage a society of continuous renovation within the organization. By encouraging workers to recognize and attend to inefficiencies, companies can make step-by-step modifications that lead to substantial performance gains gradually. Executing tools such as 5S, Kanban systems, and value stream mapping can help my website streamline operations, minimize preparations, and enhance general quality in steel stamping processes.
Verdict
To conclude, the utilization of advanced metal stamping innovations, automated processes, quality assurance actions, technology for accuracy improvement, and implementation of lean manufacturing practices are essential for making the most of efficiency and quality in steel marking procedures. These methods make sure that products are produced with cost-effectiveness, accuracy, and consistency. By incorporating these advanced techniques, producers can stay competitive in the industry and meet the needs of consumers properly.
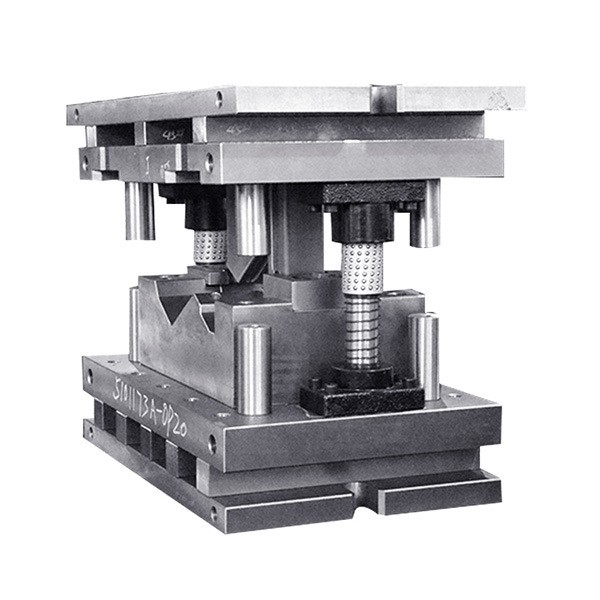
Provided the emphasis on constant top quality and performance attained through automated processes in metal marking procedures, executing durable quality control procedures becomes essential to maintain criteria and guarantee precision in stamped components. Implementing tools such as Five, Kanban systems, and value stream mapping can aid improve procedures, reduce lead times, and boost overall quality in steel stamping procedures.
In conclusion, the use of advanced metal stamping innovations, automated processes, top quality control procedures, technology for precision enhancement, and application of lean production practices are vital for making the most of effectiveness and top quality in steel marking operations.